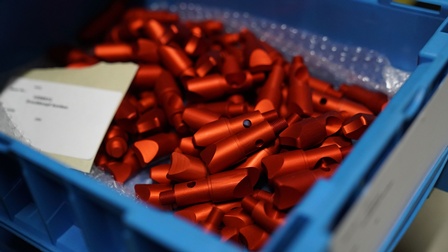
Zukunftsfittes Zerspanen in Zell am Ziller
Das Familienunternehmen Langesee ist seit einigen Jahrzehnten Zulieferer für die Industrie und zeigt, dass Metallverarbeitung nachhaltiger ist.
Lesedauer: 4 Minuten
Wo gehobelt wird, fallen Späne – zumindest bei der Firma Langesee sind diese aus Metall. Denn in Zell am Ziller zerspant das Unternehmen seit Jahrzehnten Teile für Industriebetriebe, konkret für die Bereiche Hydraulik, Maschinenbau, Optik und Sensortechnik. Das war nicht immer so, denn bei der Unternehmensgründung 1963 spezialisierte sich Hans Langesee sen. auf Keilriemenscheiben für die Heizungs- und Klimatechnik. „Mein Vater hat eine stufenlos verstellbare Keilriemenscheibe entwickelt und dafür sogar ein Patent angemeldet. Nur auf ein Produkt zu setzen, war ihm auf Dauer aber zu riskant, deswegen hat er nach einigen Jahren mit der Lohnfertigung von Drehteilen aus Metall begonnen“, sagt Hans Langesee, der das Unternehmen 1996 übernommen hat.
Diese Diversifizierung hat sich ausgezahlt: Während das Geschäft mit den patentierten Keilriemenscheiben durch billigere Konkurrenz aus dem Ausland auslief, konnte das Unternehmen die Bandbreite bei der Lohnarbeit ständig erweitern. Seit den 1990ern setzen Langesee und seine zwölf Mitarbeiterinnen und Mitarbeiter dabei auf CNC-Maschinen, also programmierbare Präzisionsmaschinen, die auf einen hundertstel Millimeter genau arbeiten. „Wir haben es aber auch schon geschafft, auf sechs- bis neuntausendstel Millimeter genau zu drehen“, sagt der Geschäftsführer.
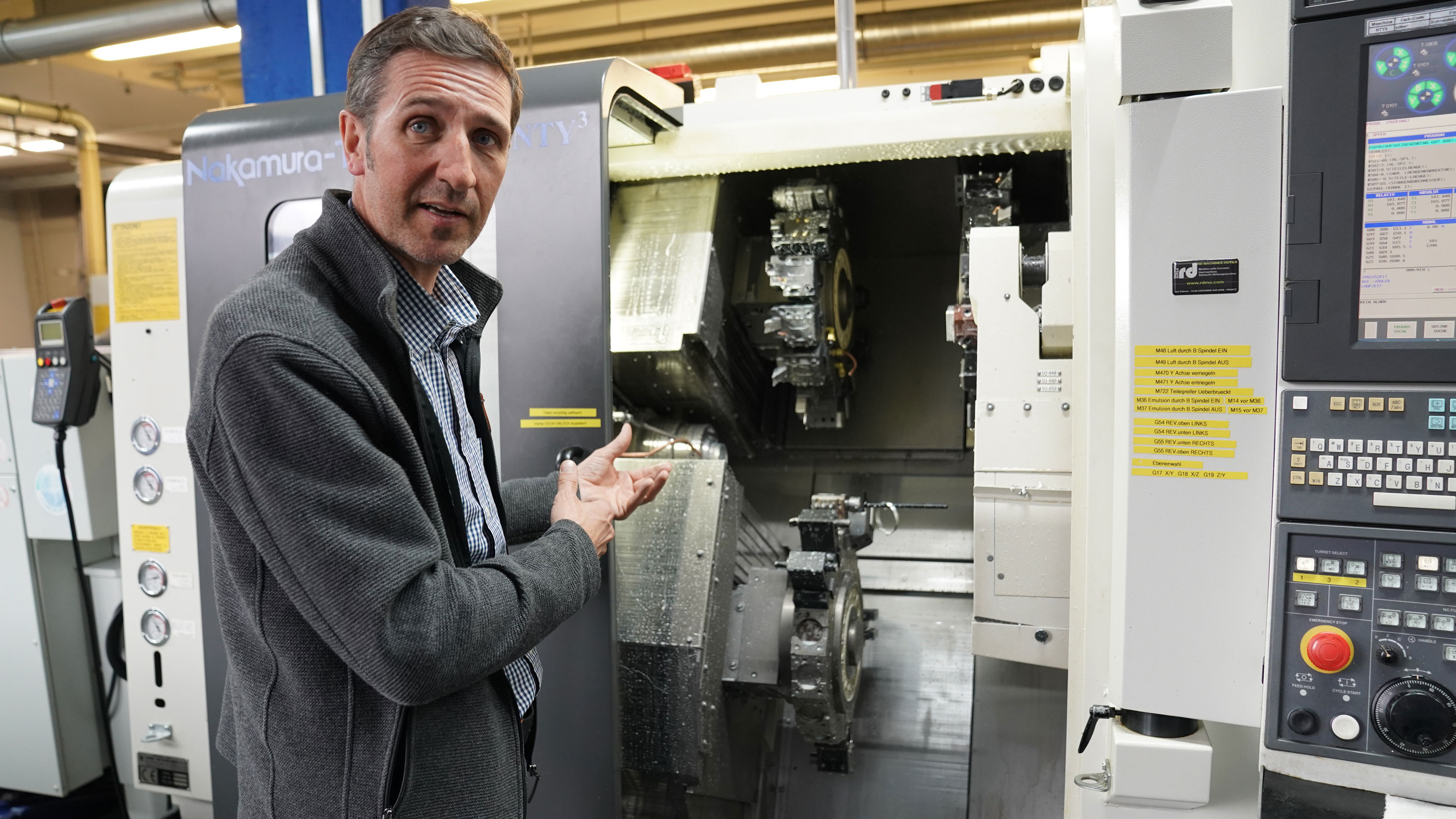
Gelebte Kreislaufwirtschaft
Die Firma Langesee produziert Losgrößen zwischen 100 und 5.000 Stück und arbeitet mit verschiedensten Metallen wie Edelstahl, Stahl, Aluminium oder Messing bis zum Kunststoff. Neben der Zerspanung von Teilen, die exakt nach den Zeichnungen der Kunden gefertigt werden können, bietet das Unternehmen auch Zusatzverarbeitungen durch Partnerbetriebe, wie Beschichtungen und Wärmebehandlungen. Der Großteil der Kundschaft stammt dabei aus ganz Österreich. Und obwohl die meisten Kunden auch international arbeiten, handelt es sich dabei um mittlere Unternehmen und keine Großkonzerne, was Langesee freut: „Der direkte Kontakt zu unseren Kunden ist uns wichtig. Denn falls es einmal Probleme gibt, müssen diese auch rasch gelöst werden. Das ist die Flexibilität, die wir als Familienbetrieb bieten: Geht nicht, gibt’s nicht!“
Was es bei dem Zeller Zerspanungsbetrieb kaum gibt, ist Restmüll: Sämtlicher Abfall, der bei der Produktion anfällt, wird wiederverwertet. Die Metallspäne gehen zurück an die Produzenten und werden eingeschmolzen; der Kühlschmierstoff, der die hochpräzise Maschinenarbeit überhaupt erst ermöglicht, wird jeden Abend aus den Maschinen gepumpt und gereinigt. Falls er irgendwann zu verschmutzt ist, geht auch dieser an den richtigen Entsorger und wird dort aufbereitet. Sogar die Putzlappen für Öl und Schmierstoffe werden gesammelt, von einem Partnerbetrieb gereinigt und erneut verwendet. „Ich bin der Meinung, dass KMU durchaus nachhaltig arbeiten. Allein schon, weil wir dort leben, wo wir arbeiten. Deswegen ist die Entsorgung bei uns im Haus transparent und nachvollziehbar“, sagt der Zillertaler, dessen Haus direkt neben der Produktionshalle liegt.
Ein zweites Standbein
So wie damals sein Vater, setzt Hans Langesee auf Diversifizierung als Zukunftsstrategie: Mithilfe eines Patents ist er dabei, sich ein zweites Standbein im Bereich Seilbahnwartung aufzubauen: „Bei Gondeln ist die Wartung der Buchsen in den sogenannten Gehängelagerungen zeit- und arbeitsintensiv. Wir haben ein Gerät entwickelt, das diesen Prozess schneller, effektiver und effizienter durchführt.“ Laut ihm ist diese Reibahle, auch Reamer genannt, das weltweit einzige Produkt, das diese Nische bedient. Bis nach Taiwan hat es das innovative Gerät deshalb bereits geschafft.
„Der Reamer macht derzeit nur einen kleinen Teil unseres Geschäfts aus, hat aber noch viel Potenzial. Derzeit mangelt es eher an der Manpower, das Produkt weiterzuentwickeln“. Auch die Firma Langesee leidet unter Nachwuchsmangel, der die meisten Branchen vor große Herausforderungen stellt. „Wir hatten schon einige Schüler und Jugendliche zum Schnuppern da, aber langfristig ist uns keiner geblieben. Wir wissen auch nicht, was den Nachwuchs von der Metallbau-Branche abschreckt oder welche Anreize wir noch konkret setzen sollen. Wenn andere Betriebe den Führerschein finanzieren oder gleich ein Studium bezahlen, kommen wir Kleineren da nicht mehr mit“. Für seine eigene Nachfolge ist zumindest gesorgt: Sein Sohn Felix ist nach der Matura in den Betrieb eingestiegen und arbeitet seitdem fleißig mit. „Er hat aber noch etwas Zeit“, schmunzelt der zukünftige Senior-Chef.
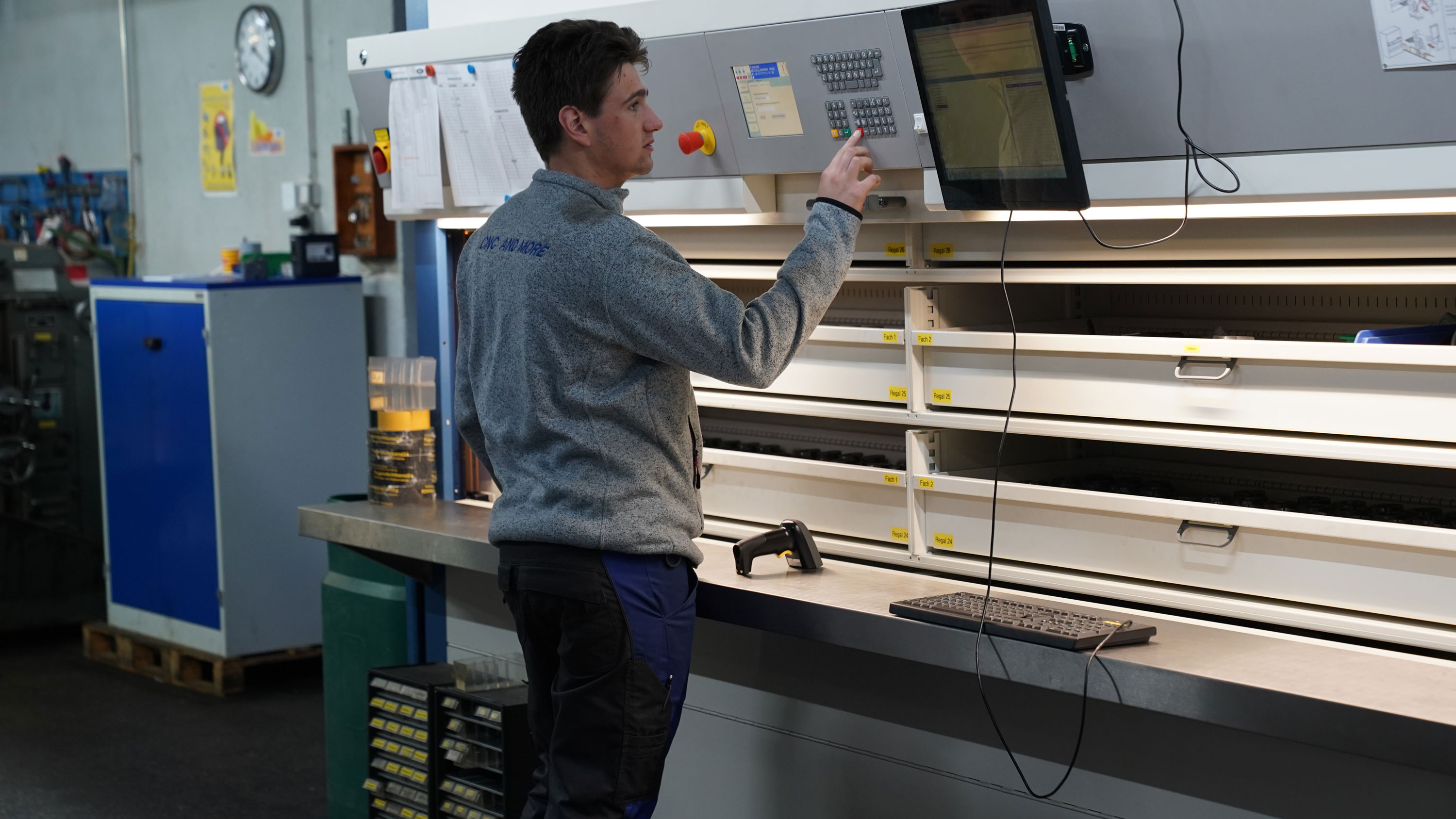
Kühlung aus dem Boden
Neben dem Nachwuchsmangel setzt sich der Unternehmer mit einer weiteren zukunftsweisenden Frage auseinander: Wie kann ein Betrieb, der mit der energieaufwändigen Metallverarbeitung sein Geld verdient, nachhaltiger wirtschaften? „Der Staat kann es nicht allein richten, wir sind alle für unsere Umwelt verantwortlich. Jeder muss sich beim Schopf packen und seinen Teil leisten“. Das hat Langesee vergangenes Jahr getan, indem er seine Produktionshalle mit einer Grundwasserkühlung im Sommer und einer Wärmepumpe für den Winter ausgestattet hat: „Wir hatten an Spitzentagen bis zu 34 Grad in der Halle. Inzwischen pumpen wir im Sommer kaltes Grundwasser durch Paneele an der Decke und erreichen ungefähr 26 bis 27 Grad – das ist gerade richtig, um sich nicht zu verkühlen. Im Winter heizen wir über diese Paneele mit unserer Wärmepumpe. Dadurch haben wir uns ein Stück weit ‚dekarbonisiert‘, weil wir unsere Ölheizung entfernen konnten und so etwa 2.500 Liter Heizöl pro Jahr einsparen.“
Dieses Jahr soll noch eine Photovoltaikanlage auf dem Dach folgen, um den Verbrauch der beiden Pumpen für das Kühl- und Heizsystem sowie etwa ein Viertel des Produktionsbetriebes zu decken. Und schon jetzt profitiert die Produktion vom Umstieg auf erneuerbare Energie: „Mit dem Kühlsystem können wir Temperaturschwankungen in der Produktion reduzieren, eine Maschine haben wir direkt an das System angeschlossen. Damit verhindern wir unkontrollierte Materialausdehnungen und garantieren, dass unsere Produkte auch auf den hundertstel Millimeter genau bearbeitet sind“, sagt der Metallfachmann. Damit im Zillertal auch nur genauso viele Späne fallen wie der Kunde wünscht
Weitere Informationen: Langesee GmbH